ピッキング作業は倉庫業務とは切っても切り離せない関係にあるものなので、それぞれの特徴や効率化するための方法を知っておくことは大変重要なことです。
この記事では、物流倉庫で行われているピッキングの種類やピッキング作業を効率化するための方法を具体的な業務内容を交えてご紹介していきます。
物流代行を始めようとしているECショップ運営者の皆さまにも物流倉庫でどういう作業が行われているのか参考になるはずです。
おさらい:倉庫業務で欠かせない「ピッキング」とは
はじめに、そもそもピッキングとはどういう作業なのかをおさらいしましょう。
ピッキングは、受注伝票やピッキング指示書に基づいて、指定された商品を保管されている倉庫の場所から取り出す作業のことです。
ピッキングされた商品はその後、梱包・検品作業が行われ、お客さまのもとへと出荷されていく流れとなります。
ECショップ事業者にとって、物流代行を利用する場合であっても大まかなピッキングの種類や必要性を理解しておく必要があります。
ピッキングの種類とそれぞれのメリット・デメリットについて解説
では次に、ピッキングの種類やそれぞれのメリット・デメリットについて解説していきます。
ピッキングには大きく分けて「シングルピッキング」と「トータルピッキング」の2つがあります。
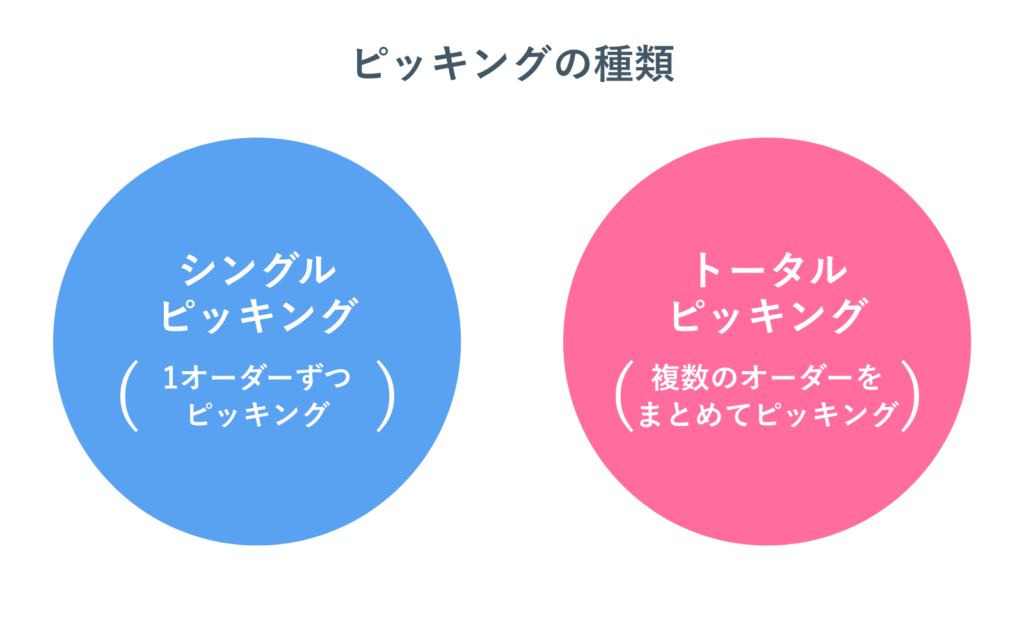
シングルピッキング(摘み取り方式)
シングルピッキングは「摘み取り方式」とも呼ばれるピッキング方法です。
この方法では、1つのオーダーごとに商品のピッキングを行います。
オーダーの数だけ倉庫を行き来する必要があるため、SKUが多いが出荷件数が少ない場合に適しているピッキング方法とされており、一般消費者向けECショップの物流センターで広く取り入れられています。
シングルピッキングのメリットとしては
- 作業内容が単純であること
- ピッキング後、商品の仕分けが不要で直接梱包に移れること
が挙げられます。
一方、作業員が動き回る範囲が広いため、移動距離が長くなり、無駄な移動や作業が発生しやすくなるというデメリットが存在しています。
(例:同じ商品が10人によって1つずつ注文されている場合、10回その商品の棚まで移動しピッキングする必要がある。)
トータルピッキング(種まき方式)
トータルピッキングは、「種まき方式」「総量ピッキング」とも呼ばれるピッキング方法です。
この方法では、複数の受注に対して注文が入った商品をまとめて棚からピッキングし、その後受注別に仕分け・梱包を行います。出荷件数は多いが、商品のSKU数が少ない場合に適したピッキング方式とされています。
(例:同じ商品が10人によって1つずつ注文されている場合、その商品の棚まで移動するのは1回で良い。そのタイミングで10個商品をピッキングする。)
トータルピッキングの最大のメリットは、まとめてピッキング・梱包を行うので、効率的に作業ができることです。
まとめてピッキングをした後の仕分け作業を行うスペースが必要になることや、まとまった受注が入らないと効率性が上がらないことがデメリットであるため、SKU数が多く、1SKUあたりの受注数が少ない場合には、シングルピッキングの方が適しています。
ピッキング作業を効率化する方法3つと、それぞれの具体的な業務内容とは?
従来のピッキング業務といえば、ピッキングリストを紙で印刷し、そのリストを見ながら商品の保管場所を探し、ピッキングを行う、という流れが一般的でした。
しかし、その方法では倉庫の保管場所を覚える必要があることや、ピッキングミスが発生しやすいことを受け、近年ではシングルピッキング・トータルピッキングどちらにおいても、倉庫業務の効率化が進められてきています。
そこでここからは、ピッキング作業の効率化方法として代表的な方法を3つご紹介し、それぞれを導入した場合の具体的な作業の流れについても解説していきます。
効率化の方法1:バーコード・ハンディターミナルを利用する
1つ目の効率化の方法としてご紹介するのは、商品バーコードとハンディターミナルを利用して行うピッキング方法です。比較的簡単に導入できる方法なので、現在多くの物流現場で用いられています。
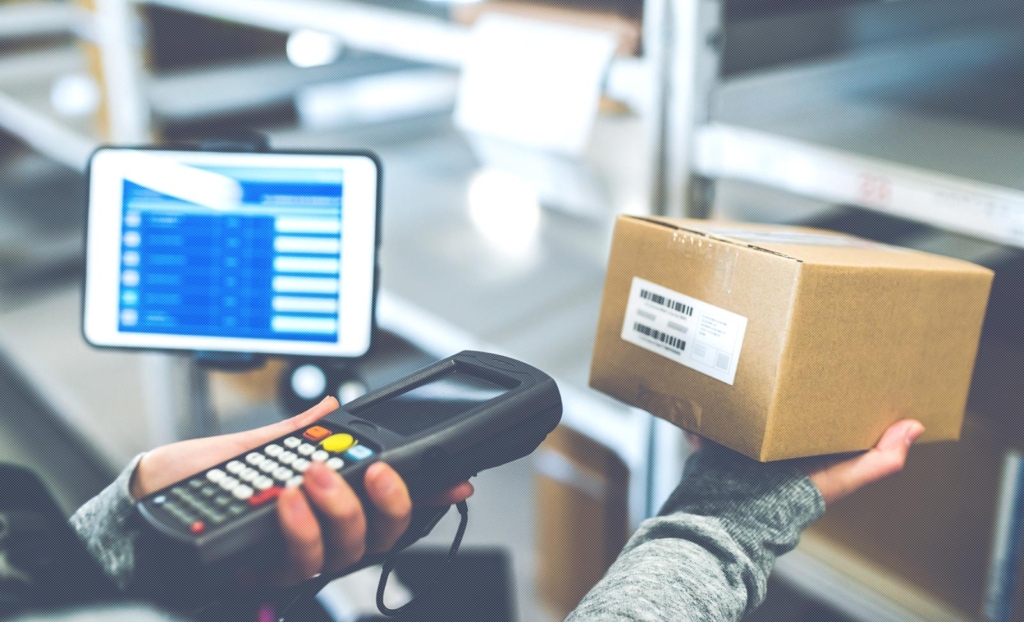
この方法の場合、
- 「ハンディターミナル」と呼ばれる専用の機械に【商品情報】と【棚の位置情報】の紐付け登録を行う
- 商品にバーコードを貼り付ける
といった作業が事前に必要となります。
実際にピッキングするときには、ハンディターミナルで
- ピッキングした商品のバーコード
- ピッキングリストに記載されているバーコード
を読み取って照合し、商品に間違いがないかを確認します。
バーコードをハンディターミナルで読み取ったときに、間違った商品バーコードの場合はエラー音でわかるようになっており、ピッキングミスの削減が期待できる方法です。
また、ピッキングリストに記載されたバーコードを読み取ることで、ハンディターミナル上で保管場所を確認することも可能です。これにより、倉庫作業に慣れていない人でも、保管場所を探し回る手間が省け、効率化にも繋がります。
効率化の方法2:RFIDを利用する
2つ目の方法としては、RFIDを利用したピッキング方法があります。
RFIDとは、専用タグと読み取り装置の間で電波を交信させ、情報を読み書きするシステムのことです。
作業者が専用の機械でタグ情報を読み込み作業を行うので、バーコード・ハンディターミナルを用いた効率化と近い方法ですが、バーコード・ハンディターミナルよりも幅広い情報を一度に読み取ることができるため、商品のピックアップがより効率的になるとされています。
効率化の方法3:デジタルピッキングシステムを利用する
3つ目にご紹介するのは「デジタルピッキングシステム(DPS)」を利用する方法で、こちらは上述した2つの方法とはかなり異なった方法です。
デジタルピッキングシステム(DPS)とは、デジタル表示器を使いピッキングを効率化するための作業支援システムのことです。この方法を導入する場合には、事前準備として商品が保管されている棚にデジタル表示器を取り付け、システムとの連携を行います。
ピッキングする時には、
- ピッキングリストは不要
- 作業者はランプが光った場所の商品を、表示された数だけ取り出す
といった流れとなります。
紙のピッキングリストを使った場合と比較して、表示器の指示に従ってピッキングを行えば良いので
- 人のミスを防止し、正確性・効率性を高めることができる
- 商品を知らなくても表示器の指示に従えばいいので、熟練した技術・ノウハウがいらない
といったメリットがあります。
一方で、導入時のシステム費用が比較的高く、バーコード・ハンディターミナルを利用する方法に比べて導入例は多くはありません。SKU数が多く、出荷件数も多い倉庫などでは、作業効率を高めるために導入されている事例があります。
まとめ
この記事では、倉庫業務とは切っても切り離せない関係にある「ピッキング」について、種類や効率化の方法をご紹介してきました。それぞれの特徴について理解したり、具体的な業務イメージを持っていただけていれば幸いです。
今回のポイントをまとめます。
- ピッキング種類は大きく分けて「シングルピッキング」「トータルピッキング」の2種類があり、出荷件数や取り扱いSKUに応じて適したものを選ぶ必要がある
- ピッキングの効率化方法として「バーコード・ハンディターミナル」「RFID」「デジタルピッキングシステム」の3つが代表的で、導入することでミスの削減や作業スピードの上昇に繋げられる
当社が提供するEC自動出荷システム「LOGILESS」でも、ピッキング効率化が可能となるように
- ハンディターミナル
- バーコードスキャナ
のデバイスに対応しており、最小限のコストで庫内作業を効率化することができます。
EC自動出荷システム「LOGILESS」の概要についてわかりやすく解説した資料もご用意しています。倉庫内の業務効率化に興味がある方や、LOGILESSのことを知りたい方は、ぜひダウンロードしてみてくださいね。